The construction industry is facing a major labor shortage, with fewer workers available to meet growing project demands. In 2022 alone, US contractors lost an estimated $30 billion to $40 billion due to inefficiencies caused by workforce challenges. With aging tradespeople and fewer young people entering the industry, companies are looking for ways to do more with fewer workers. So, what are some of the options for tackling these issues?
One solution that is gaining traction is Lean construction — a method focused on improving efficiency, reducing waste and increasing productivity on jobsites.
Lean principles are not new — having a long history in the manufacturing sector — but the application of these principles to construction is a newer concept. This is due to the high complexity and wide degree of variance between construction projects.
Two key Lean construction methods helping companies navigate labor shortages are pull planning and the Last Planner System® (LPS).
What is pull planning?
Pull planning is a planning technique that starts with the end goal in mind. Instead of following a rigid, top-down plan, teams develop a workback schedule together using key project milestones. By involving key on-site workers — such as project managers, subcontractors, trades and suppliers — early in the planning process, teams can avoid project delays, reduce wasted effort and ensure tasks are completed in the right order.
Push planning (Traditional)
- Schedule centrally planned by one individual or team
- Rigid timelines based on past needs or forecasted demand
- Excess time buffered to handle unforeseen delays
- Excess resources needed to handle unforeseen bottlenecks
Pull planning (Lean)
- Schedule dynamically constructed by teams responsible for completing work
- Milestones set based on customer deadlines
- Flexibility on how to hit milestones
- Less buffer time required
- Less resources wasted
The Last Planner System
The Last Planner System is a more holistic approach to construction management that includes pull planning, collaborative decision-making and continuous improvement. The name is derived from the importance of including Last Planners® — those closest to a job being completed — in the decision-making process.
It includes five key steps:
- Should do — Identifying what tasks need to be done.
- Can do — Checking if tasks can realistically be completed with available resources.
- Will do — Assigning tasks and making commitments.
- Did do — Reviewing what was completed.
- Learn — Reflecting on what worked well and what needs improvement.
By following these steps, teams can adapt to changes more easily and prevent costly mistakes.
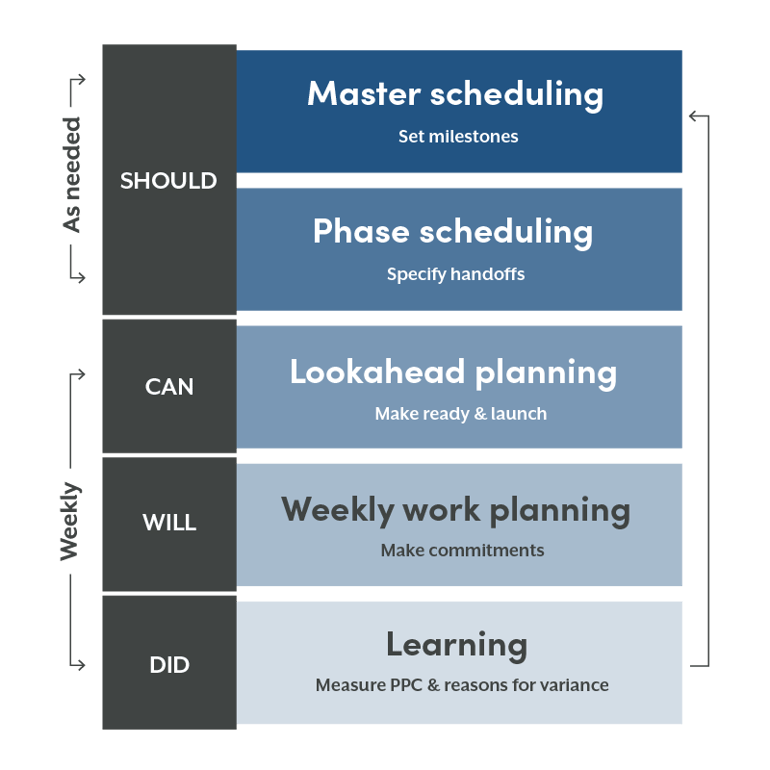
Stages of the Last Planner System
How Lean construction helps with labor shortages
While Lean construction can’t solve the labor shortage on its own, it helps construction firms work smarter by:
- Improving workflows — Streamlining processes so tasks are done in the most efficient way.
- Boosting productivity — Making sure workers are focusing on value-added tasks instead of waiting for materials or redoing work.
- Reducing waste — Cutting down on unnecessary steps, material waste and delays.
By using Lean construction methods, companies can get more done with fewer workers, helping them stay competitive despite workforce challenges. However, the labor shortage also requires long-term solutions, including investment in employee training and retention.
How to implement Lean construction in your projects
If you’re interested in using Lean construction principles, here are some ways to get started:
- Start with small changes — Apply pull planning and the LPS® to one project or even one phase of a project to see the benefits before expanding it across all operations.
- Use digital tools — Introduce digital tools to help teams stay connected, provide real-time updates, reduce waste and improve communication between workers, managers and stakeholders. These tools allow for better tracking of progress, identification of bottlenecks and quick adjustments to schedules when unexpected challenges arise.
- Train your team — Educate workers on Lean principles and give them an active role in planning and problem-solving.
- Improve communication — Hold daily or weekly check-ins with teams to adjust plans based on real-time challenges and opportunities.
- Measure results — Track productivity, material use and project timelines to identify areas for improvement.
- Set benchmarks — Make sure project goals are outlined and the team is aligned on goals so everyone sees the big picture. Setting benchmarks allows transparency for the team to see what they’re aiming to accomplish.
The bottom line
By improving efficiency through pull planning and the Last Planner System, construction firms can keep projects on schedule and make the most of their available workforce. While Lean principles can’t fully address the need for more skilled workers, they offer a practical way to adapt to the current labor market and set the industry up for long-term success.
Tools for Lean construction
Interested in going digital with the Last Planner System? We have just what you need.
Posted on Mar 31, 2025 6:00:00 AM